Introduction
O-Rings are widely used in various industries, including hydraulic, pneumatic, automotive, aerospace, and electronics. Their primary function is to create a seal between two or more components, preventing the leakage of liquids or gases. However, if an O-Ring fails, it may lead to leakage, equipment damage, or even safety hazards. Therefore, understanding the common causes of O-Ring failure and their prevention measures is crucial for improving sealing performance and extending service life.
1. Compression Set
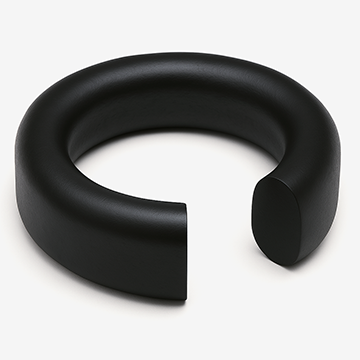
Failure Symptoms
After prolonged compression, the O-Ring loses its elasticity and fails to return to its original shape, resulting in reduced or failed sealing performance.
Possible Causes
- Excessive operating temperature: High temperatures accelerate rubber aging, causing the O-Ring to lose elasticity.
- Prolonged compression: Continuous compressive stress exceeding the material’s elastic limit leads to permanent deformation.
- Improper material selection: Choosing a material that is not resistant to the medium or temperature can result in performance degradation.
Prevention Methods
- Select materials with low compression set: Such as FKM, HNBR, which maintain good elasticity at high temperatures.
- Control compression ratio: Ensure that the O-Ring compression ratio is within the recommended range (typically 15-30%) to prevent excessive compression.
- Regular replacement: Avoid prolonged static compression by periodically inspecting and replacing O-Rings.
2. Hardening & Cracking
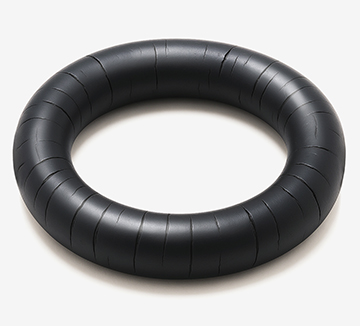
Failure Symptoms
The O-Ring hardens, develops cracks, or becomes brittle, leading to sealing failure.
Possible Causes
- Long-term exposure to high temperatures or ozone: These factors accelerate rubber aging.
- Use of non-heat-resistant materials: For example, NBR tends to age and degrade in high-temperature environments.
- Contact with strong oxidizing chemicals: Substances like acids, alkalis, or cleaning agents can cause material degradation.
Prevention Methods
- Select materials resistant to high temperatures and chemicals: Such as FKM, EPDM, which offer excellent resistance to high temperatures and chemicals.
- Minimize ozone and UV exposure: Store and use O-Rings in controlled environments to reduce exposure to these factors.
- Avoid contact with strong oxidizers: Choose chemically resistant materials and consider isolation measures in design.
3. Extrusion & Nibbling
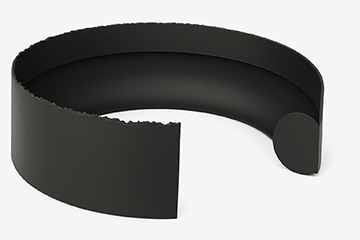
Failure Symptoms
The O-Ring is extruded out of the groove under pressure, causing edge damage or tearing.
Possible Causes
- Excessive sealing gap: Leads to O-Ring extrusion.
- Excessive system pressure: Exceeds the material's pressure resistance limit.
- Low O-Ring hardness: Inability to withstand high-pressure conditions.
Prevention Methods
- Reduce the sealing gap: Ensure design compliance with standard recommendations (typically <0.15mm).
- Use O-Rings with higher hardness: Such as 80 Shore A or higher to improve extrusion resistance.
- Add back-up rings: In high-pressure environments, using backup rings prevents O-Ring extrusion.
4. Abrasion
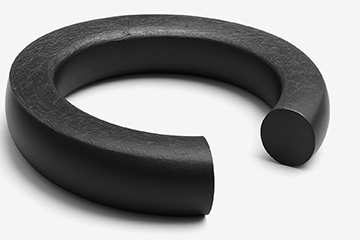
Failure Symptoms
The O-Ring surface shows significant wear marks, reducing sealing performance.
Possible Causes
- Relative motion between the seal and metal surface: Causes continuous friction and wear.
- Insufficient lubrication: Results in direct contact friction between the O-Ring and moving surface.
- Improper surface treatment: Increases wear on the O-Ring.
Prevention Methods
- Use Special Recipe: Such as internal lubricants to reduce friction.
- Choose high-wear-resistant materials: Such as PU, HNBR O-Rings.
- Optimize sealing design: Minimize unnecessary movement contact and ensure smooth surfaces to reduce friction.
- Select the correct sealing component: Depending on the application, choose O-Rings with low-friction characteristics.
5. Chemical Degradation

Failure Symptoms
The O-Ring swells, deforms, or experiences surface erosion, leading to seal failure.
Possible Causes
- O-Ring material is incompatible with the working medium (e.g., NBR in contact with ketone solvents).
- Prolonged exposure to strong acids, bases, or solvents, leading to material decomposition or swelling.
- External environmental factors, such as high temperature and pressure, accelerate chemical reactions.
Prevention Methods
- Select chemically resistant materials: Such as FKM, FFKM, EPDM.
- Test O-Ring compatibility with the medium to ensure material suitability for the application.
- Consider protective coatings or sealing structure modifications to minimize direct chemical exposure.
6. Swelling & Shrinkage
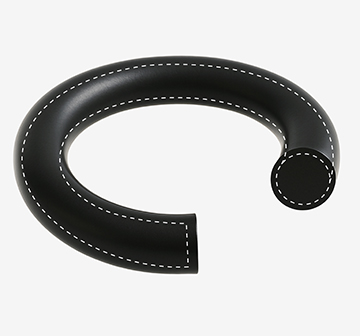
Failure Symptoms
The O-Ring absorbs liquid and expands, or shrinks due to solvent evaporation, affecting sealing performance.
Possible Causes
- Material absorbs liquid, causing volumetric expansion and reduced sealing effectiveness.
- Prolonged exposure to solvents, leading to material component loss, resulting in shrinkage or hardening.
- Alternating environmental conditions, causing dimensional instability.
Prevention Methods
- Use materials with low absorption properties, such as FKM, FFKM or PTFE.
- Limit O-Ring immersion time in incompatible liquids to prevent excessive swelling.
- Select appropriate sealing solutions based on application requirements, such as additional protective layers or pre-treatment techniques.
7. Thermal & Pressure Cracking
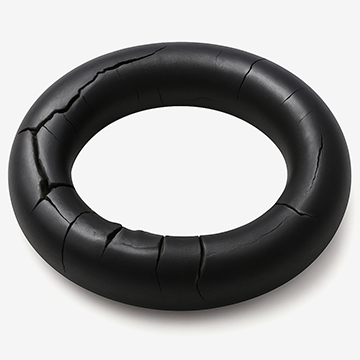
Failure Symptoms
The O-Ring surface develops fine cracks, or even ruptures, leading to seal failure.
Possible Causes
- Extreme temperature fluctuations, leading to internal stress accumulation and cracking.
- Sudden pressure changes in the system, exceeding the O-Ring's pressure tolerance, causing rupture.
- Material is not resistant to thermal shock or pressure variations, e.g., NBR becomes brittle at low temperatures.
Prevention Methods
- Choose high-temperature-resistant materials, such as FKM, HNBR.
- Control system pressure fluctuations to avoid sudden changes that create stress concentrations.
- Ensure proper O-Ring installation to minimize additional stress during assembly.
8. Installation Damage
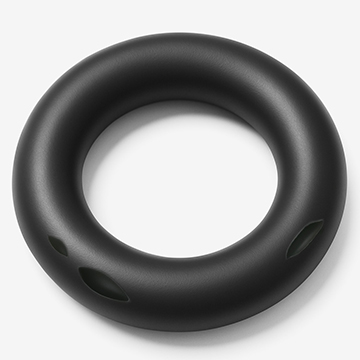
Failure Symptoms
The O-Ring tears, scratches, or deforms during installation, resulting in compromised sealing performance.
Possible Causes
- Improper installation techniques, such as excessive stretching or use of incorrect tools.
- Contact with sharp edges, causing surface damage.
- Incorrect O-Ring size or type, leading to installation difficulties and sealing inefficiencies.
Prevention Methods
- Use proper installation tools to avoid excessive stretching, and apply lubricants for easier installation.
- Check installation surfaces for sharp edges or burrs to prevent O-Ring damage.
- Ensure O-Ring dimensions match the sealing groove to prevent excessive compression or deformation.
Conclusion
By understanding these eight major causes of O-Ring failure, including compression set, hardening and cracking, extrusion, abrasion, chemical degradation, swelling, thermal cracking, and installation damage, we can implement effective preventive measures to enhance sealing performance and extend service life.
For more information on O-Ring selection, applications, or technical support, please contact GMORS. Our professional team is ready to provide material recommendations, technical assistance, and sealing solutions tailored to your specific needs. Whether for standard products or custom applications, GMORS is committed to delivering high-quality sealing solutions to ensure reliable and stable equipment performance.